Drying malt barley for acceptance
July 7, 2020
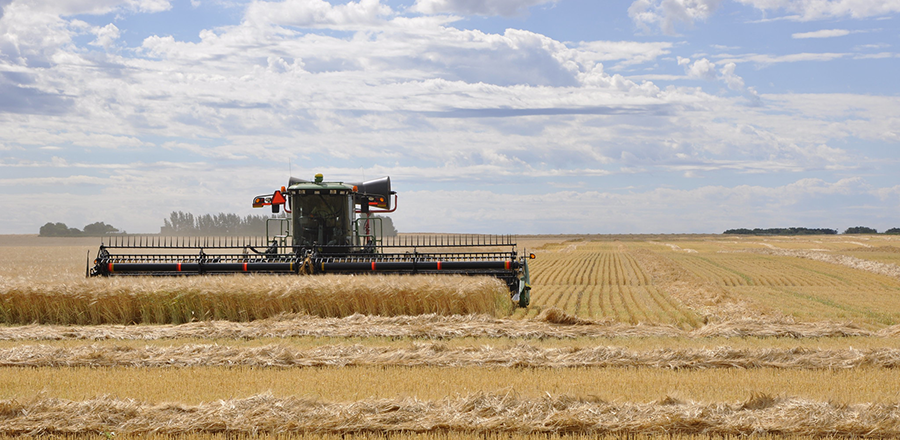
Grain moisture can make or break a barley crop’s chance of being accepted for malt. With maltsters demanding a maximum 13.5 to 14.5 percent moisture, grain drying is a serious consideration for malt barley growers.
“It’s a decision that needs to be made by the grower and really depends on their specific situation,” says Lorne Grieger, Project Manager, Agricultural Research & Development, Prairie Agricultural Machinery Institute (PAMI). “Not all growers have a dryer set-up, but many do benefit from having one – it’s added insurance to maintain quality for malt barley.”
The decision to use a dedicated hot air grain dryer was an easy choice for Scott Keller of Keller Farms Ltd. in New Norway, Alberta.
“We put 100 percent of our malt barley through the grain dryer every year,” he says. The dryer allows him to take control at harvest regardless of what Mother Nature has in store; he can harvest his grain earlier at higher moisture levels knowing that the dryer will take care of the work.
Keller operates a 2,500-acre grain farm with wheat, peas, fava beans and canola in his rotation. All of his barley is straight cut and sent to the dryer right from the field. He says the decision to dry all his barley is tied to the conditions in his central Alberta region. “Growers in the southern part of the province can leave their barley standing and it will get dry. But a typical harvest for us is rain every few days and it just never gets dried out.”
Protecting quality
It all comes down to quality for Keller. “The longer you leave barley to weather in the field, the worse it is. The sooner you can get it off, the better the quality. Laying it in the swath is problematic on our farm. When the swath stays wet, then those grains sprout. Maltsters typically have a zero tolerance for sprouted barley. Without that grain dryer we wouldn’t be very successful malt barley growers.”
Keller’s rule of thumb is to combine the barley once the grain moisture content is 18.5 percent or less and then use the dryer to get it down to 13 percent. “Quite often we’re storing some of our barley for nine to 12 months. I find that if it’s at 13.5 percent, it can sometimes be problematic for germination. I target 13 coming out of our dryer,” he says, adding that it takes just one pass in the dryer to reach this level.
Keller makes sure to keep the dryer heat low for best results. “You can’t dry malt barley as hot as other grain because it may damage germination. We run our flame temperature at 145℉ for barley whereas our wheat gets dried at 180℉.”
Drying capacity
It’s a system that’s been working for the Kellers for the past 25 years. Purchased by his dad in the mid-nineties for about $35,000, the Vertec dryer runs cost-efficiently on natural gas. Over the years they’ve added an elevator leg and two more bins to increase capacity.
Keller estimates the system dries about 500 bushels an hour. “The dryer is an appropriate size for a one-combine farm like ours. It’s very rare that we’re not able to dry whatever's been combined in a day within 24 hours. Basically, the wet bin is empty before there’s another load of grain back to the yard.”
The decision to put up an elevator leg meant that the dry auger was no longer needed to feed the bins. While it is more expensive, Keller says the leg has paid off when it comes to his malt contracts. “Augers can be tough on the grain. Since putting up the leg, we’ve had less peeled, broken and damaged kernels, which maltsters appreciate.”
Keller calculates that it would cost about $250,000 to replace his dryer set-up today. He believes the investment is well worth it for his operation – from both a cost and time perspective.
“It doesn’t make sense for us to wait for dry grain to dry naturally. We’ve had significant snow and cold, rainy weather during our last five harvests, but we made the most out of every day and combined every chance we could. We wouldn’t have been able to do that without our grain dryer.”
Don’t wait until fall
Keller’s system is just one of the many possible set-ups that malt barley growers can consider for their farm.
An alternative to Keller’s dedicated hot air dryer is an in-bin system. “You’re actually doing the drying process inside the bin,” explains Grieger. “The key components are a fan and supplemental heat. You can also dry grain within the bin without adding heat. If you have the right conditions outside, if your ambient temperatures warm up, and if humidity is low enough relative to your grain, you can extract the moisture just by adding the outside air to it.”
How do growers know which system to choose? It really depends on where the farm is located and what conditions they have to contend with. With 2019 harvest conditions posing challenges across the Prairies, Grieger believes many growers will be exploring whether a dryer is a suitable tool for their operation going forward.
“One thing I always recommend at this time of year is to prepare now,” Grieger says. “Don’t wait until fall. This is the time to start asking the questions and get ready for the different scenarios that may come this harvest.”
Pre-harvest grain dryer tips
A leading cause of fire in grain dryers is lack of maintenance. Get your dryer ready for a safe and successful harvest with these tips:
1. Clean the dryer’s exterior and interior to remove all debris that may block airflow or affect operation.
2. Lightly lubricate any areas prone to high wear or rust.
3. Carefully clean the control boxes with soft brushes, a vacuum, and/or compressed air.
4. Inspect the electrical components for indication of overheating or physical damage.
5. Check all electrical connections to make sure they are tight. A systematic tightening at first start-up and a re-tightening every 10 years thereafter will help maintain proper operation.
6. Carefully check gas supply lines, burner, vapourizer, and burner gas train for leaks. Make sure all are clean and free of debris, particularly the burner gun or exit area. Make sure any rubber hoses are in good condition. Replace every 10 years or according to local gas ordinances.
7. Inspect all motors and ensure they are securely fastened in place; lubricate bearings, if applicable, but do not over-lubricate.
8. Check all belts to make sure they are in good shape, properly tensioned, and that all safety shields are present.
9. Inspect all ladders and platforms to ensure they are safe to use.
10. Lubricate any bearings that are not permanently sealed.
11. Lubricate all chains and check for proper tension.
12. Check any gearboxes for oil level and change out the oil according to the dryer’s maintenance schedule.
13. If repairs are necessary, use a qualified service technician.
14. Do a test run before harvest to make sure everything runs properly.
Source:
AGCO